Trenchless force main work minimizes public disruptions
The Regional Municipality of York, located north of Toronto in Ontario, is one of the fastest-growing municipalities in Canada. The region recently completed construction of a Force Main Twinning project, with GHD Ltd. as design engineer and Ward & Burke Microtunnelling Ltd. as general contractor. This project helped to enhance the operational flexibility and resiliency of their sewage collection system, all while maintaining service and minimizing construction impacts to the local community.
Previously, all of the discharge flow from the region’s 7 million gallons per day-Bogart Creek Sewage Pumping Station (Bogart SPS) was conveyed through a single 18-inch Bogart force main approximately 1,600 feet in length, which was installed by open cut trench excavation in 1991. The contract scope for the recent Force Main Twinning project included construction of a new 18-inch Bogart force main (FM) in parallel with the existing force main in order to provide redundancy for this key element of the region’s collection system and allow for the existing force main to be taken out of service for maintenance after more than 30 years of continuous operation.
The new Bogart FM terminates into a separate new 42-inch force main that was also constructed under the same Force Main Twinning project. The project received funding from Infrastructure Canada through its Disaster Mitigation and Adaptation Fund (DMAF) program.
Open-trench vs. trenchless
Both open-trench and trenchless (e.g., microtunnelling) methods were originally evaluated for installation of the new Bogart force main. Some of the relative points of comparison for assessing the two approaches included:
Trenchless technologies like microtunnelling involve more specialized work, which may limit qualified bidding competition for certain areas/projects.
The overall efficiency of trenchless operations, as well as the level of project risk, can vary depending on subsurface ground conditions and other details of the proposed utility alignment.
Trenchless technologies allow surface disturbance from construction to be concentrated at select sending and receiving sites.
Trenchless installation typically permits the resulting utility profile to pass under potential surface obstructions (such as buildings, roads, rail tracks, utilities, water bodies, and sensitive environmental areas) and to be independent of the local land topography.
The larger 42-inch line proposed under the Force Main Twinning project was determined to be particularly well-suited for installation via microtunnelling. In the case of the new 18-inch Bogart FM, the initial ratings for the open-trench and microtunnelling alternatives were much closer, with each offering a different set of advantages and risks.
The Bogart force main cut through a residential neighborhood that would be heavily impacted for over a year if open-trench construction was selected. Most of that disturbance could be avoided by applying microtunnelling technology.
However, the anticipated tunnel drive featured up to 60 feet of cover over the pipe, a high groundwater table, very dense silty till soils with cobbles and boulders, and minimal free space for a receiving shaft site, which meant more challenging conditions for microtunnelling operations. The smaller tunnel diameter could also further increase the level of risk, due to the reduced equipment capacities and limited accessibility to the microtunnel boring machine (MTBM) for possible maintenance and repairs during a drive.
As both the open-trench and microtunnelling options were considered to be similarly fitting for construction of the project, GHD ultimately prepared the project bidding documents assuming primarily open-trench installation as a more conventional baseline approach, which the region had more historical experience with. However, additional provisions, such as sharing the previously collected geotechnical data for the potential microtunnel profile with prospective bidders, were included to maintain flexibility for the proposed construction method.
Ward & Burke Microtunnelling Ltd. (WBML) was the successful bidder for the project, and it submitted a no-cost change proposal to install the new Bogart force main primarily by microtunnelling instead of open-trench excavation. This scenario altered some of the key decision factors that were previously weighed to determine the proposed construction method.
First, WBML had a proven track record of microtunnelling in similar conditions as those anticipated for the Bogart force main, including prior work with York Region. Since microtunnelling was proposed as a change during construction, GHD — as engineer and construction manager — was able to request and perform detailed review of WBML’s project-specific work plan, which included the use of interjacks as well as 1200 mm inside diameter (ID) reinforced concrete microtunnel pipe (RCMP) with enough capacity to achieve a safety factor of over 3.0 at the estimated maximum jacking force of 1,900 kN. Furthermore, the change proposal indicated that WBML would take on the potential risks associated with the microtunnelling approach without increasing the project cost for the region.
Safety risks & social burdens
As expected, the utilization of microtunnelling technology for installation of the force main offered substantial benefits. Perhaps most notably, by microtunnelling below the densely populated residential areas and roads along the pipe alignment, the potential safety risks to both the general public and contractor’s personnel as well as local social burdens associated with open-trench excavation over the same length (including open excavations, lane/road closures, construction noise and visibility, possible damage to private property and/or existing utilities, etc.) could be significantly reduced or even eliminated.
The local topography required steep pipe slopes, an intermediate high point, an air release valve with corresponding vault, and an inline back pressure sustaining valve for the original open-trench profile.
In contrast, the microtunnelling approach allowed for a flatter profile with a consistent slope and no intermediate high point. This in turn reduced the head on the upstream sewage pumps under normal operating conditions by about 17%, thereby decreasing facility power costs and increasing the maximum flow capacity of the existing pump station by 20%.
The consistent slope also made draining/flushing of the force main easier, and eliminated the air release valve and back pressure sustaining valve that otherwise would have been a significant long-term maintenance burden.
Hydraulic modeling optimizations
During review of the Bogart microtunnelling proposal, GHD worked with the region and WBML to perform updated system hydraulic modeling of the alternate force main profile and develop recommended modifications to the Bogart SPS facilities to accommodate the revised configuration, including force main termination details, shaft site layout, automatic control programming, and standard operating procedures. For example, the allowable operating speeds for the existing pumps had to be adjusted to keep them on their rated performance curve while running under the decreased discharge head.
Following a collaborative and adaptive effort that leveraged the collective experience of the project team, the proposed plan to install the new Bogart force main via microtunnelling was finalized and subsequently accepted by the region based on the recommendation of GHD. As a related bonus, the region elected to expand the scope of the Force Main Twinning project and have WBML install a second new Bogart FM within the same microtunnel pipe.
Such opportunities to simultaneously construct multiple utility lines through a single tunnel can boost the overall cost-effectiveness of the application, and in this case will allow the region to eventually replace the aging existing force main at a fraction of the cost that it would have taken to do so under a separate future project. The final microtunnelling arrangement of the new facilities also combines the long-term corrosion resistance of HDPE force main pipes within the structural protection of RCMP.
The new Bogart force main was constructed via microtunnelling ahead of the original project schedule despite restrictions related to the COVID-19 pandemic, and with minimal disruptions to the residential areas that would have otherwise been heavily impacted for over a year by installation of the same via open-trench excavation.
The experiences from successful completion of the Force Main Twinning project, and installation of the new pipe in particular, provides a case study on the recommended design considerations and potential benefits of utilizing the latest microtunnelling technology for linear infrastructure projects.
Jason VerNooy, P.E. is a water/wastewater project manager with GHD based out of Bowie, Maryland. Jason has more than 14 years of experience in the design and construction of municipal water and wastewater treatment facilities in the Mid-Atlantic region and beyond, including linear infrastructure. Jason can be contacted at (240)-206-6843 or [email protected].
About the Author
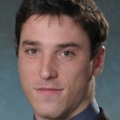
Jason VerNooy
Jason VerNooy, P.E. is a water/wastewater project manager with GHD based out of Bowie, Maryland. Jason has over 14 years of experience in the design and construction of municipal water and wastewater treatment facilities in the Mid-Atlantic region and beyond, including linear infrastructure as well as facility-wide upgrades at wastewater pumping stations and advanced treatment plants with rated capacities ranging from 0.25-30 mgd. Jason can be contacted at (240)-206-6843 or [email protected].