How to employ liners and coatings to protect underground assets
Maintaining the longevity of critical water and wastewater infrastructure in public utilities remains paramount. The United States, with more than 153,000 public drinking water systems and more than 16,000 wastewater treatment facilities, increasingly focuses on extending the lifespan of critical infrastructure.
For example, consider Illinois American Water's 2023 investment of $297 million in water and wastewater infrastructure — a testament to the need for proactive maintenance strategies that extend the service life of these systems and delay costly repairs.
By employing advanced coating and lining systems, municipalities can protect their critical underground wastewater infrastructure against the elements and defend against corrosion and degradation. Consider these key strategies to safeguard underground assets effectively and secure long-term reliability.
First, define coatings and liners
Professionals often use "coatings" and "linings" interchangeably, yet significant differences exist between them.
The Association for Materials Protection and Performance (AMPP) defines a coating as a material applied up to 0.125 inches (125 mils), forming an adhesive bond with the substrate, such as concrete. In contrast, a lining exceeds this thickness and may be bonded or unbonded.
Those tasked with specifying and designing underground utility protections must regard this distinction as vital to ensure everyone works from the same playbook.
The benefits of polymeric liners and coatings
The primary role of a polymer lining or coating is to extend the service life of the underground infrastructure. These materials work as a barrier that resists chemical corrosion, abrasion and high-velocity water impact. The protection can also prevent groundwater infiltration into structures like manholes.
For instance, routine comprehensive inspections of decades-old manholes with a protective coating system reveal robust structural integrity with no apparent defects or leaks. These evaluations, which include adhesion tests, demonstrate the coating's effective performance, a testament to the high-quality application and strict quality control standards.
Protection also offers aid in visual inspections. Lighter-colored coatings can improve the visibility within structures.
Another role of polymer lining or coating includes protecting against microbial-induced corrosion (MIC). MIC remains one of the most aggressive threats to concrete structures in wastewater systems.
The Thiobacillus bacteria causes MIC. Thiobacillus bacteria excrete sulfuric acid, which leads to accelerated concrete degradation. High turbulence or stagnant flow within the sewer system can cause Thiobacillus bacteria to thrive. The smell of sewer gas can indicate a stagnant system and the presence of MIC, which should ideally be absent from an effectively functioning system.
Also, the concentration of sulfuric acid is indicated by the pH levels, and this, by extension, reflects the health of the underground infrastructure. The protective products must withstand acidic environments where pH can plunge to well below three. At this level, rapid concrete deterioration begins.
Select the right solution
When selecting the appropriate protection, one must assess the environment, the structure's material (for example, manholes can be made from block, brick or concrete), the structure's condition and its intended use (the demands on a manhole in a residential neighborhood differ from those near a high-flow lift station).
Today's marketplace offers a variety of options, such as high-build and thin-film epoxies, elastomeric and moisture-curing polyurethanes, polyurea hybrids and pure polyureas.
One factor to consider in the selection process includes a structure's moisture. Generally, these products adhere well to dry concrete. Still, high-build epoxies excel in adhesion, making them ideal for saturated surface dry (SSD) or moisture-laden surfaces.
However, experts steer clear of polyureas and polyurethanes for SSD concrete due to its vulnerability to moisture, which can lead to a foaming reaction. Experts recommend drying the structure and applying a suitable primer to mitigate this, with tri-hybrid polymer coatings proving effective, especially when paired with a primer in damp conditions.
Professionals must also balance the need for tensile strength and flexibility. While high-build epoxies boast tensile strengths ranging from 5000 to 8000 psi, coatings like polyurea, polyurethane and tri-hybrids offer more flexibility, albeit with a lower bond strength.
In static structures such as manholes, professionals prioritize bond strength over flexibility since they typically endure minimal movement. Yet, for scenarios involving significant movement, the flexibility of the coating can be paramount to maintain the integrity of the underground infrastructure.
Other factors include hydrostatic and soil stresses, traffic and live load. For example, traffic induces the most significant stress on vertical structures like manholes, primarily affecting the cover and frame. Although intense at the surface, this stress diminishes with depth, so select materials for the cover to withstand these loads.
Always choose the right polymer liner or coating based on recommendations from the product manufacturer, backed by historical case study performance and third-party testing.
Surface preparation, specifications and quality checks
After selecting, make certain to take these steps to help ensure the effectiveness of the coating and lining system.
Particularly, a well-formulated specification remains the blueprint for a successful protection application. It lays down the foundational requirements for product thickness, surface profile and post-application inspections.
The foundation of a successful coating application lies in meticulous surface preparation. 90% of coating failures occur due to poor surface preparation. Adhering to industry standards, such as AMPP standards, in specification preparation ensures a baseline quality for surface preparation, cleaning and coating.
Post-preparation inspections, such as substrate pH checks, remain important. The substrate pH should be neutral or slightly above to ensure a clean surface. The surface profile, as defined by the International Concrete Repair Institute (ICRI), should ideally range between three and six, depending on the manufacturer's specifications.
Successfully applying a coating requires cleanliness and thoroughly removing existing coatings, dirt and debris. Use only certified, trained and qualified installers.
The rigor of quality assurance (QA) and quality control (QC) protocols, from adhesion testing (ASTM D7234) to pinhole detection, cannot be overstressed. These checkpoints validate the integrity of the coating system, preventing potential failures. Specifying minimum coating thickness and post-application QA and QC testing, including density and moisture level, adhesion, pinhole and mil thickness checks, provides excellent product performance.
For example, PPG Protective & Marine Coatings inspected a 16-year-old manhole protected with its Raven Lining Systems in Cedar Park, Texas, and found no visual defects or active leaks. The inspection included pulling tests on the coating, indicating its strong adherence to the structure thanks to its high performance, application and QA/QC practices.
Find the right coatings partner
The continuous evolution of coating and lining technologies goes hand in hand with the future of wastewater infrastructure maintenance. Partnerships among manufacturers, engineers and applicators enhance the effectiveness of these protective solutions.
That's why partnering with an expert coatings and linings provider remains critical to extending the life of expensive underground wastewater infrastructure. Such collaboration facilitates informed choices for surface preparation, specifications and quality practices, ensuring underground wastewater infrastructure integrity and readiness for forthcoming challenges.
About the Author
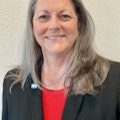
Kathy Romans
Kathy Romans is the water and wastewater segment manager for the PPG Protective and Marine Coatings business. With 25 years of wastewater and water industry experience, Romans has been at the forefront of pioneering solutions safeguarding vital infrastructure.