Four considerations for large pump station design
Large pump station design is complex. Not only does a design have to be feasible — it also must be developed thoughtfully to ensure long-term success.
Pump stations that address combined sewer overflows (CSO) typically have high pumping capacities and are very deep (usually more than 100 feet below ground). There are only a handful of CSO storage tunnels across North America. It is critical to consider the long-term operation and lifecycle costs when undertaking a large pump station design.
Stantec is continuing work with the Northeast Ohio Regional Sewer District (NEORSD) to design the third and final tunnel dewatering pump station for its CSO program, which has been in progress for 13 years.
The Southerly Tunnel Dewatering Pump Station (STDPS) will be used to dewater 54 million gallons per day and will be located in a 65-foot diameter shaft with screening and grit collection.
STDPS is similar to NEORSD’s other tunnel dewatering facilities, where it can expect a high collection of solids and intermittent use depending on the frequency and intensity of storm events, given that it only operates to address wet weather. NEORSD’s tunnel dewatering pump stations range in depth from 180 to 240 feet and corresponding capacities from 36 to 160 million gallons per day (MGD).
CSO pump stations of this depth and complexity are rare. They are often in areas of old infrastructure using combined sewers. These facilities have unique challenges related to material and solids handling, and they require a highly skilled and experienced design team.
For utilities and municipalities planning to undertake large pump station projects, there are several key design considerations for peak performance and longevity. While this article will briefly consider each point individually, it is important to note that they need to be considered in a collaborative environment, with input from several design disciplines. Since each of the following points influences another, it is vital to take a fully integrated approach to large pump station design.
1. Proper Pump Selection
As pump stations of this size and depth are rare, proper pump selection is critical. The range of required dewatering volumes and corresponding head conditions can vary dramatically. For example, with the STDPS project, 25% of the anticipated storm events in a typical year will amount to 150,000 gallons or less. The same facility will also need to dewater as much as 54 million gallons of water within 24 hours when the tunnel is full.
As the liquid level in the tunnel and shafts drop during dewatering, a nearly infinite number of operating points along a pump’s curve can be expected. If not properly accounted for, a pump can run out of its preferred operating range, greatly reducing its performance and life expectancy. This can be avoided using either variable frequency drives or control valves to keep the pump in its ideal operating condition. Having the means to adjust the pump to meet the widely varying operating conditions is critical to long term success of the pumping station.
2. Intermittent Use of Pumping Equipment
Another consideration is the intermittent use of the pumping equipment, given that these wet-weather-only stations are typically operated after it rains — possibly as few as 20 times a year. Depending on a utility’s available capital and operating budget, it is also helpful to consider long-term operations and maintenance practices. For example, utilities must think through the need for permanently installed handling equipment. Given that pumps are typically pulled once a year for routine maintenance, does it make more sense to have an annual pump maintenance contract with crane rental instead of training staff and investing in specialized, higher capacity cranes?
Also think about the planned occupancy of the pump station. Is there a need to house pumping and screening facilities fully enclosed indoors? If so, these CSO stations are typically rated as Class I, Division 1 hazardous spaces, requiring explosion-proof equipment and higher ventilation rates that can significantly increase capital and long-term operating costs.
3. Power and Demand Requirements
When it comes to the power and demand requirements for these types of pump stations, there is a lot to consider.
First, look at the pumping power usage and costs. These pump stations require large pumps with motors in the hundreds — sometimes even thousands — of horsepower each. Power usage will be minimal when the station is not running but could see a major spike during high-flow events. Since electrical costs are based on usage and demand, electric bills could vary dramatically month to month depending on the number of pumps operating and the duration. Electricity bills can be minimized by reducing the dewatering rate — thus reducing electrical demand — when weather conditions permit a longer dewatering period for the tunnel before the next wet weather event.
Also think about HVAC power usage. To meet the NFPA 820 requirements (the standard for fire protection in wastewater treatment and collection facilities), HVAC systems may use more power during the year than the pumps themselves. This situation depends on the location of the station, since the standard can require several air changes per hour where outside air may have to be heated during the cold winter months. During design, decisions will need to be made regarding costs for these HVAC operations and maintenance versus construction costs for explosion-proof equipment because the degree of room classification is tied to air change rates when applying NFPA 820. Due to the size of equipment in these stations, it is important to coordinate with the local power utility to provide sufficient power capacity and appropriate redundancy for the electrical power distribution system. It may take the utility significant time to supply the site with adequate power for the station, and the work could negatively impact the overall project schedule.
4. Solids and Debris Management
Solids build-up in CSO tunnels, particularly grit, is a real concern. Grit accumulation in CSO tunnel systems is inevitable. Design and maintenance strategies can be employed to minimize grit accumulation and protect equipment like pumps and isolation gates. Typically, utilities opt for either grit removal or grit transport. At a minimum, CSO tunnels incorporate coarse bar or “trash” racks to prevent large debris from blocking critical flow paths or damaging pumps.
With pump station design, especially for deep CSO applications with a lot of potential debris, evaluate all the options for managing solids. One option could be investing in dedicated screening equipment that rakes and collects debris. However, these systems are large, complex, expensive and require additional operating costs for regular maintenance, hauling, and more.
Inevitably, grit will make its way to the pumps. Grit has been known to wreak havoc on CSO pump stations to the point where they have been clogged even from startup. A dedicated flushing system will help mitigate this, using potable water or by recirculating a portion of the pumped flow to help resuspend and mix any settled grit and debris.
Another option is to implement a final dewatering strategy to flush the system by operating the pumps in a specific sequence to help “self-clean” the wet well. However, this could be a costly undertaking and lead to a large monthly electric bill because of the large size of the pumps, and the potential electric demand charge associated with the operation of those pumps.
Whichever strategy is selected, this is another example where the lifecycle costs of the system cannot be overlooked. Should you invest in large, expensive equipment that requires routine maintenance now, or pay for spikes in electrical charges each time the pumps are run for “self-cleaning”?
Helping Communities Address CSO Challenges
Each of these elements play into one another and are important factors in the design and operation of large-scale pump stations.
With extensive experience in large pump station design, Stantec has developed a deep understanding of what successful design entails. As the Stantec team begins its design for the STDPS and evaluates the work it has done on the other associated pump stations, the designers are considering many of these same aspects. Helping communities address their CSO challenges is important work, and a well-designed large pump station will play an important role in the process.
About the Author
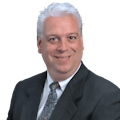
Doug Reed
North American Electrical Discipline Lead for Stantec Water
Doug is a North American Electrical Discipline Lead for Stantec Water. He has over 36 years of experience in the planning, design and construction administration of electrical systems for water and wastewater treatment and conveyance facilities throughout the US. He is located in Stantec’s Cleveland, Ohio office.
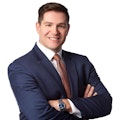
Vito Cimino
Senior Principal - Water/Wastewater Conveyance
Based in Stantec’s Cleveland, Ohio, office, Vito is a veteran project and design manager overseeing the successful delivery of large and complex wet weather projects. An experienced tunnel dewatering pump station engineer, he has spent a majority of his career working on combined sewer overflow and collection system related projects.