Manage wastewater odors with plant-based neutralizers
It is an understatement to assert wastewater treatment agencies have their hands full with responsibilities.
Not only are they tasked with collecting, treating, and safely discharging refuse to the environment, but they must do so in a manner compliant with numerous laws, regulations, and ordinances. On top of these challenges, recognition is rarely ascribed, because when the job is done right, the public barely notices the agency’s presence.
However, managing foul odors is an increasingly relevant issue for wastewater facilities, and a task that — if conducted unsatisfactorily — is sure to attract unwanted attention. As residential and commercial development expands over time, unpleasant odors can quickly create issues as neighborhoods and wastewater treatment sites converge in proximity.
Left unaddressed, complaints proliferate, and these often result in negative press or even regulatory consequences. In the era of social media, this type of negative publicity can happen faster than ever before, and with more widespread and heightened consequences.
Some wastewater facilities that did not have these sorts of problems in the past due to their distance from neighboring developments are now finding themselves in this situation. These facilities frequently turn to conventional odor control techniques initially, but these masking methods are far from ideal, as they tend to overpower one unwanted smell with another, instead of addressing the root cause.
In contrast, modern plant-based natural neutralizers work by chemically altering the molecules responsible for malodors, rendering them impotent. Common offenders in the wastewater industry include hydrogen sulfide, sulfur dioxide, skatoles, indoles, and amines —but individual facilities have varying odor control needs.
Rather than providing a one-size-fits-all answer, leading odor control experts can formulate and prescribe solutions addressing specific facility needs, with solutions based on thorough laboratory analysis.
Limitations of conventional methods
Of the various conventional odor control methodologies — including masking agents, chemical scrubbers, adsorption and carbon filters, ozone, and biological filters — most have critical shortcomings (Figure 1).
Some use hazardous materials, while others only work on certain types of odors, and a handful are simply ineffective. Additionally, many of these methods require expensive equipment, materials, setup, and maintenance to disperse mitigants, sometimes from multiple vendors, and these systems are often unwieldy and costly to operate.
In contrast, plant-based neutralizers are safe, require relatively little equipment, and are effective in almost every odor-removal application because they use custom formulations designed to treat specific odors.
Research-driven formulation of plant-based neutralizers
Designing an effective plant-based solution requires identifying the molecules responsible for malodors at the facility in question. First, gas samples are collected at the process site and stored in Markes-thermal desorption tubes. These tubes, when compared to conventional Tedlar bags, provide longer sample life — several weeks versus 24 hours — while remaining effective at lower sample volumes.
After collection, samples are analyzed via gas chromatography mass spectrometry (GC-MS) to determine precise molecular composition (Figure 2).
The GC-MS analyzer produces a chromatogram, which plots detector response (y-axis) against retention time (x-axis). Each peak in the chromatogram represents the quantity of each substance detected, including those which cause malodors (see Figure 3 below).
Armed with this information, scientists formulate specific blends of plant oils to neutralize the substances of concern.
In this way, every product prescription is tailored to the specific needs of each client for optimal odor control.
Atomization and vaporization delivery systems
Sometimes these neutralizers can be used with existing odor control hardware, such as scrubbers. For all other circumstances, atomization or vaporization systems are installed to distribute odor removers in the specific locations where they are needed.
Atomization systems
Atomization systems mix water for dilution with concentrated formulations, spraying the mixture into locations of concern to neutralize odors on contact. These systems provide a great deal of flexibility and control over dispersion, including spray volume and surface area. In addition, the use of concentrated products requires less storage space and reduces shipping costs because water, added on site, accounts for most of the weight and bulk after mixing.
There are two ways for atomization systems to disperse odor remover.
In large open-air settings, high-pressure hydraulic systems forcefully propel droplets, making them effective for treating gas emissions and surface vapors.
Conversely, in confined spaces, low-pressure systems that spray the mixture through a fan are sufficient. Fan systems have the advantage of portability for easy transportation to multiple areas in a facility.
Vaporization systems
In contrast to atomization systems, vaporization systems pump pre-mixed formulations through perforated pipes as dry vapor. These solutions arrive on site ready-to-use, and do not require water dilution prior to application. These dispersion considerations ease operations and maintenance requirements, but vaporization may not be suitable in particularly humid environments.
Vaporization systems can distribute odor removers at rates of anywhere from 50 to 2,400 cubic feet per minute. Compared to atomization systems, they distribute smaller droplets, resulting in higher odor absorption, and they do not use nozzles, reducing maintenance requirements as nozzles can plug (Figure 5).
In many cases, odor control systems do not need to be run constantly. To optimize operations and only run equipment when required, sensors can quantify odor concentration in real time. Leveraging these measurements, control systems can vary the dispersal rate of odor remover for best performance and lowest operating cost.
Remote monitoring and control
To facilitate operational flexibility, cloud-based interfaces, such as Ecosorb’s EcoLink, can provide remote access to atomization and vaporization systems through a secure cloud server. These software tools empower operators to:
- Remotely start, stop and change system operating mode;
- Identify low product levels;
- Track and trend flow rates, energy use, downtime and other key performance indicators.
- Send alerts and notifications;
- Adjust product dosage to coincide with fluctuating odor-producing periods;
- Encrypt data for transit and storage; and
- View metrics, charts and diagrams on an intuitive dashboard.
Authorized users can access the interface from a computer, tablet, smartphone or any other device capable of supporting a web browser, enabling them to make informed operational decisions at any time from any location.
Case study: Reducing complaints by implementing odor control
A wastewater treatment plant in the Southeast U.S. operated successfully for decades, earning awards from U.S. EPA and regional groups for their commitment to sustainable wastewater treatment and discharge.
When the plant was built, the surrounding area was largely undeveloped, and odor control was hardly a consideration. But, over time, residential communities emerged nearby, closing in on the facility.
New neighbors began complaining about the odors from the plant, which included a constant musty, dirt-like smell from the activated sludge process, in addition to more obnoxious odors periodically produced during biosolid digestion and belt filter press operation (Figure 6).
To maintain their reputation and show commitment to serving the community, the plant needed an effective mitigation solution.
At the recommendation of a sister municipality, the plant engaged Ecosorb to conduct a site study and propose a plant-based formulation to treat its malodors. The team identified concentrated Ecosorb 610 as the solution for the agency’s airborne smells. Just five gallons of product supply the plant for two weeks, with each gallon diluted in 37 to 55 gallons of water. The mixture is then distributed as a fine mist via atomization systems in impacted areas.
Atomized droplets electrostatically attract and then break down the offending molecules, neutralizing the odors instead of masking them. In this case, the odors treated include those caused by hydrogen sulfide, sulfur dioxide, ammonia, ethyl mercaptan and methyl mercaptan.
According to plant management, the Ecosorb system is the most effective odor control solution the facility has used in its decades-long history. Since installation, complaints have dwindled precipitously.
Absolve odors and move ahead
Plant-based neutralizers are a safe, eco-friendly, and cost-efficient way to control wastewater odors. They are simple to apply and require little maintenance. They treat malodors at the source by breaking down the offending molecules.
Installing and maintaining robust odor control systems is vital to maintain pleasant neighborly relationships, freeing wastewater facilities to focus on safe and efficient treatment and disposal, instead of fielding and fighting complaints.
About the Author
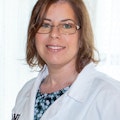
Laura Haupert
Laura Haupert, Ph.D., is the chief scientific officer for Ecosorb, where she leads research and development, regulatory, safety, and quality control. She earned her B.S. in chemistry from Manchester College and Ph.D. in physical chemistry at Purdue University, working with bond energies of solvated clusters. Haupert also completed her post-doctoral research at Purdue where she focused on the development of mass spectrometric methods for the structural elucidation of lignin catalytic degradation. Haupert has developed and directed Ecosorb’s many product lines — and she has overseen the state-of-the-art laboratory and production facility in Rising Sun, Indiana — for over ten years.