How membrane materials improvement is advancing water reuse
As citizens become increasingly environmentally conscious, global regulations, such as the Safe Drinking Water Act (SDWA) in the United States and the Registration, Evaluation, Authorization, and Restriction of Chemicals (REACH) in Europe, have introduced more stringent polices that are impacting industrial and municipal water use. Stricter requirements have included limiting allowable levels of certain types of chemicals to trace amounts and providing water testing capabilities where previously there were few to none. Companies worldwide needing to address these regulations and those that want to meet pressing sustainability goals are looking to advancements in water filtration and water reuse to meet their diverse and specific challenges.
Industry trends point to a growing demand for clean and abundant water
The scarcity of water globally continues to be an issue of critical importance. According to World Resources Institute data, nearly a quarter of the world’s population experiences high water stress, often depleting almost all their accessible water resources. By 2050, that number is predicted to increase by one billion.[1] The World Health Organization shared that in 2022, a minimum of 1.7 billion people used a drinking water source contaminated with feces.[2]
An urgent need exists for advancing mass water reuse capabilities along with efficient purification and filtration techniques aimed at producing higher-quality water. At the same time, legislative requirements and customer demands necessitate that the chemicals and processes used are environmentally conscious and not detrimental to human and animal health.
As such, chemists and innovators are working to enhance membrane technology. They are also developing cutting-edge desalination methods that effectively transform seawater or brackish water into clean freshwater suitable for different uses. They are working to enhance the efficiency of sustainably recovering industrial process water and wastewater.
Progress can be made towards cleaner, recycled and reused water if industry and academia join forces and chemical developments continue to expand at a rapid pace. Our collective well-being and future depend on those in the private and public sectors making a significant investment in water filtration technologies and advancements.
Developing solutions
Water filtration solutions must be cost-effective and remove trace amounts of contaminants such as grease and hazardous materials with disposal methods that don’t release harmful emissions. Until recently, standards in the industry involved membrane chemistries using fluorinated compounds because of their mechanical and temperature durability.
Unfortunately, one of the raw materials used in many of these membranesare so-called "forever chemicals", such as polytetrafluoroethylene (PTFE). These chemicals remain in the environment permanently and negatively impact our ecosystem. Several European Union member states, including Denmark and Germany, are looking to ban PTFEs, and others may follow. Polyvinylidene fluoride (PVDF) has been a popular alternative to PTFE, but its supply is shrinking, and thus, costs are rising, meaning it may not be a sustainable long-term solution.
How is the water filtration industry overcoming these issues to develop and implement products and processes that work? They do it through extensive research, testing and trials, and new technological advancements.
Recovering laundry water in Mexico
In Mexico City, few residents have in-home washing machines; most visit laundromats to clean their clothes. To keep up with demand, most of the city’s laundromats receive a delivery of fresh water three or four times per day at great expense to facility owners.
Virtually none of this water is reused or recycled, creating a financial burden for laundry operators and adding to one of Mexico City’s most pressing environmental problems: a massive water shortage. Climate and water experts recently expressed concerns that the region may be mere months away from what they call “day zero,” where water levels become so low that they will not have any to share with local citizens.[1]
A large chain of laundromats asked suppliers to come up with a solution to this problem.
PPG, a filtration membrane producer, worked jointly with a systems integrator to gather customer requirements, understand processes, and secure the right polymeric filtration membrane and process for the job.
PPG’s microfiltration (MF) membrane incorporated an anti-oil build-up (called antifouling) treatment technology designed to remove oil, and in this case address soapy, surfactant-laced water, so process water and wastewater could be disposed of or reused safely and cost-effectively. This helps to improve water reuse and contributes to mitigating global water scarcity. The technology is also free of PTFEs or PVDFs.
To determine if the membrane would work, the scientists first followed a course of action that began with screening a sample of the water and running it through a small-scale test to see how it performed and if it met the customer’s requirements. Then, larger-scale testing with larger membrane filters was used to determine if the solution could meet efficiency needs and hit broader targets. The systems integrator then used the solution on a pilot project to confirm that it would accomplish what it needed to do over time.
After using one laundry facility as a pilot, the MF polymeric membrane generated laundry water recovery rates of more than 70%, and freshwater use at the facility was reduced by more than 50%, producing significant cost savings for the operator. The solution has since been replicated at other laundromats, bringing even more significant financial benefits and saving considerable fresh water.
Recovering water from a car parts manufacturer
In a separate example, a car parts manufacturer aimed to eliminate fluid/oil and suspended solids from the water utilized in its cleaning operation to facilitate the recycling and reuse of the water.
The previous membrane system failed to adequately treat the water to the required standard for reuse, leading the manufacturer to resort to expensive and inefficient bag filtration methods to meet discharge regulations. Moreover, mounting pressure from the local municipality to decrease the volume of water discharged into the public water system prompted the company to explore alternative technologies for improved performance.
After PPG and a different systems integrator were brought in, an ultrafiltration (UF) membrane was determined via lab testing to be the best solution for this client.
UF membranes typically have smaller pores than MF membranes. They block the same components as MF membranes but also filter out contaminants such as viruses, finer particles, plastics, harmful toxins, and air pollutants. UF membranes are typically preferred for higher purification and separation processes.
Regarding the oil and water separation process, a common method involves the use of a spiral wound filter setup. In this setup, the oily water is pumped into one end of the filter and moves across the membrane surface.
As it does so, it separates into two streams: clean water (permeate) and concentrated oily water (concentrate). The spiral design has an advantage because the high velocity of the flowing water helps keep the membrane surface unfouled. Additionally, the pressure generated aids in the separation process by pushing clean water through the membrane. The speed at which clean water is separated is known as the flux rate, with higher flux rates critical for reaping more significant economic benefits.
Upon further testing, the car parts manufacturer’s water solution generated permeate quality that met and, in some areas, exceeded the parts manufacturer’s target and maintenance-stable flux rates. The high-flux polymeric membrane also produced clean permeate water at a recovery rate greater than 90%. The system has continued to perform at and above expectations more than a year later, lowering the amount of water entering the local water supply so that the municipality could handle the volume.
Best practices in determining water filtration solution success
Scientists, systems integrators, and filtration customers must collaborate throughout the life of a water filtration and reuse project to ensure that everyone is working with accurate data and processes. Ideally, by being transparent and communicating clearly, all parties should thoroughly understand the end user's needs and how they plan to use the system before implementation.
Suppose a pivot on technology needs to occur after initial testing or a new use case for the solution identified by the client. In that case, all of this should be well-communicated to stakeholders along with a new timeline, if necessary.
Finally, once the system is in place, proper training, consistent and accurate usage, and up-to-date maintenance are vital to ensure long-term success.
About the Author
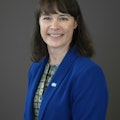
Lisa Walters
Lisa Walters is the global strategic market manager, specialty coatings and materials at PPG Industries.